Exploring Advanced Tools and Methods for Accurate Welding Evaluation
In the world of welding assessment, the quest of accuracy and integrity is paramount, stimulating the growth of innovative devices and methods. Laser scanning developments and computerized inspection systems, equipped with synthetic intelligence, are redefining the landscape by minimizing human mistake and improving security steps.
Ultrasonic Examining Developments
Ultrasonic testing technologies frequently stand for the forefront of developments in welding assessment innovations. These developments have actually dramatically enhanced the ability to spot and assess interruptions within bonded frameworks, making certain improved integrity and security - Welding Inspection Madison. Ultrasonic testing utilizes high-frequency audio waves to pass through materials, giving comprehensive information about interior attributes without creating damage. The newest growths in this area have concentrated on enhancing precision, speed, and the ability to analyze complex information.
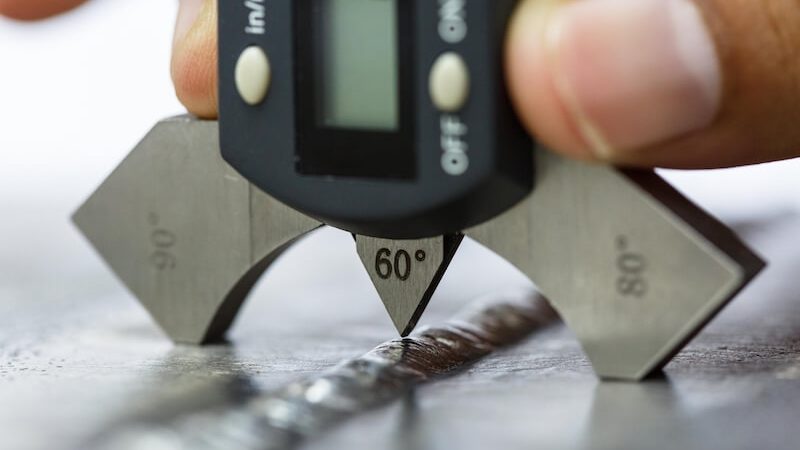
Additionally, advancements in software application algorithms for data evaluation have enhanced the precision of defect detection and sizing. Automated ultrasonic testing systems now provide high-resolution imaging, making it possible for comprehensive analyses of weld top quality. These systems are typically integrated with advanced visualization devices, which assist in the interpretation of outcomes.
Radiographic Evaluation Strategies
While ultrasonic screening developments have actually set a high criterion in non-destructive exam, radiographic examination techniques remain to play an essential role in welding inspection by supplying unique insights right into material integrity. Radiographic testing (RT) uses using X-rays or gamma rays to penetrate materials, developing a radiograph that aesthetically represents the inner framework of a weld. This imaging capability is indispensable for discovering subsurface issues such as porosity, incorporations, and fractures that might not show up via surface area assessments.
The process includes positioning a radiation resource on one side of the weld and a detector on the opposite side. Variations in product density and density affect the attenuation of the rays, generating a contrasting image that exactly marks imperfections. RT is specifically beneficial for examining thick sections and intricate geometries where various other methods may drop short.
Despite its performance, radiographic assessment should be carried out with strict adherence to safety methods as a result of the dangerous nature of ionizing radiation. The analysis of radiographs requires experienced workers, as the quality of the analysis straight impacts the dependability of the examination. Ongoing advancements in electronic radiography are improving photo clearness and interpretation performance, reinforcing RT's critical function in guaranteeing weld quality.
Laser Scanning Breakthroughs
Accepting laser scanning modern technology in welding inspection has actually revolutionized the evaluation of weld top quality and honesty. Unlike conventional evaluation methods, laser scanning provides fast information procurement, dramatically boosting the performance and precision of weld analyses.
Laser scanning advancements have actually caused significant renovations in discovering and identifying surface area defects such as porosity, absence of blend, and damages. The high-resolution data enables examiners to carry out detailed analyses, making sure that welds meet rigid market standards. This technique sustains the development of digital records, helping with long-term quality assurance and traceability.
Furthermore, laser scanning modern technology incorporates flawlessly with software application services designed for automated problem detection and evaluation. The resultant information can be quickly shared and assessed, promoting collaborative decision-making procedures. As markets remain to demand greater requirements for weld top quality, laser scanning continues to be at the forefront, supplying exceptional accuracy and effectiveness in welding assessment.
Automated Inspection Systems

Automated evaluation systems offer the advantage of uniformity, eliminating human error and subjectivity from the evaluation procedure. They are made to operate in different settings, from production floors to remote area sites, guaranteeing extensive insurance coverage. Welding Inspection Madison. These systems can be configured to abide by particular welding requirements and requirements, providing thorough reports and paperwork for quality assurance objectives
In addition, the assimilation of cloud-based systems assists in the storage and evaluation of vast amounts of assessment information. This enables pattern evaluation and anticipating upkeep, allowing manufacturers to resolve potential issues reference prior to they rise. The fostering of computerized examination systems is an essential step towards enhancing the dependability and effectiveness of welding processes in industrial applications.
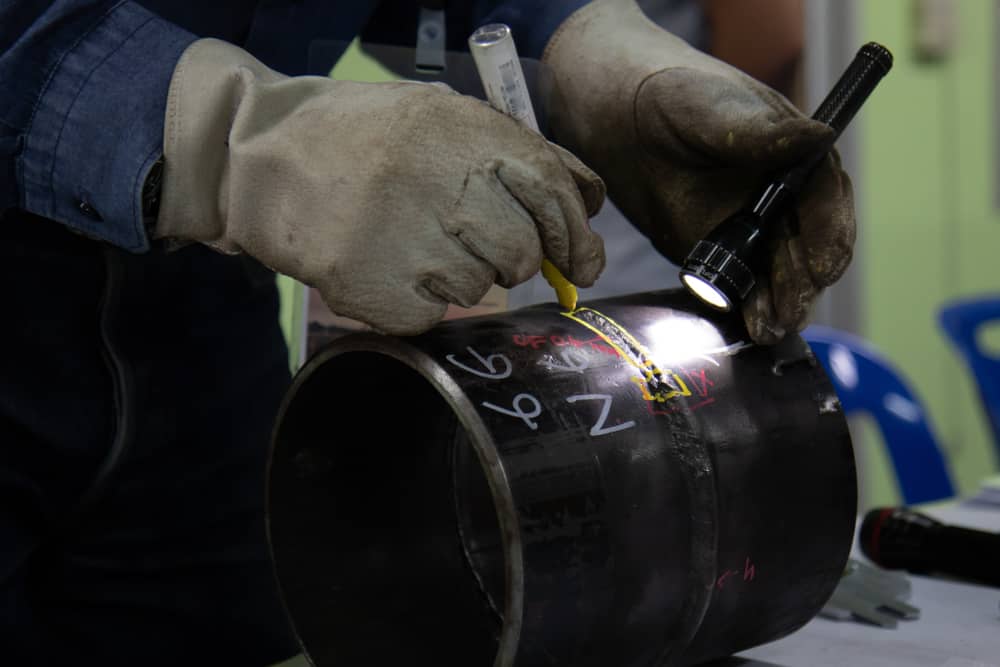
Enhancing Safety And Security and Efficiency
A substantial element of improving safety and security and efficiency in welding pop over here assessment exists in the integration of innovative innovations that enhance procedures and alleviate risks. The adoption of advanced non-destructive screening (NDT) approaches, such as ultrasonic screening, phased range ultrasonic testing (PAUT), and radiographic screening, plays an essential duty in making sure architectural integrity without compromising the safety of the employees entailed. These strategies allow for comprehensive evaluations with marginal downtime, minimizing prospective dangers connected with traditional approaches.
Moreover, the execution of real-time information analytics and device discovering algorithms has actually changed the way examination data is interpreted. By using predictive analytics, possible problems can be identified before they materialize right into important failures, guaranteeing timely treatments and upkeep. This proactive approach considerably boosts functional performance and safety in welding processes.
Additionally, remote evaluation technologies, consisting of drones and robotic spiders outfitted with high-resolution cameras, enable inspectors to analyze hard-to-reach locations without subjecting them to dangerous problems. This not only enhances examination accuracy but also decreases human danger. By leveraging these sophisticated tools and approaches, markets can achieve higher safety requirements and functional effectiveness, inevitably causing more trustworthy and lasting welding examination practices.
Conclusion
The assimilation of sophisticated tools and techniques in welding examination considerably enhances flaw detection and makes sure architectural stability. These advancements not just increase assessment performance however likewise contribute to enhanced security and top quality guarantee in commercial welding applications.

Ultrasonic screening innovations frequently stand for the leading edge of improvements in welding examination modern technologies.While ultrasonic testing advancements have actually set a high criterion in non-destructive exam, radiographic assessment methods continue to play an important role in welding evaluation by providing distinct understandings right into product honesty.Accepting laser scanning technology in welding evaluation has changed the go to my blog evaluation of weld high quality and stability. As sectors continue to require higher requirements for weld top quality, laser scanning remains at the center, providing unrivaled accuracy and performance in welding assessment.
Automated assessment systems offer the benefit of consistency, getting rid of human error and subjectivity from the assessment process.